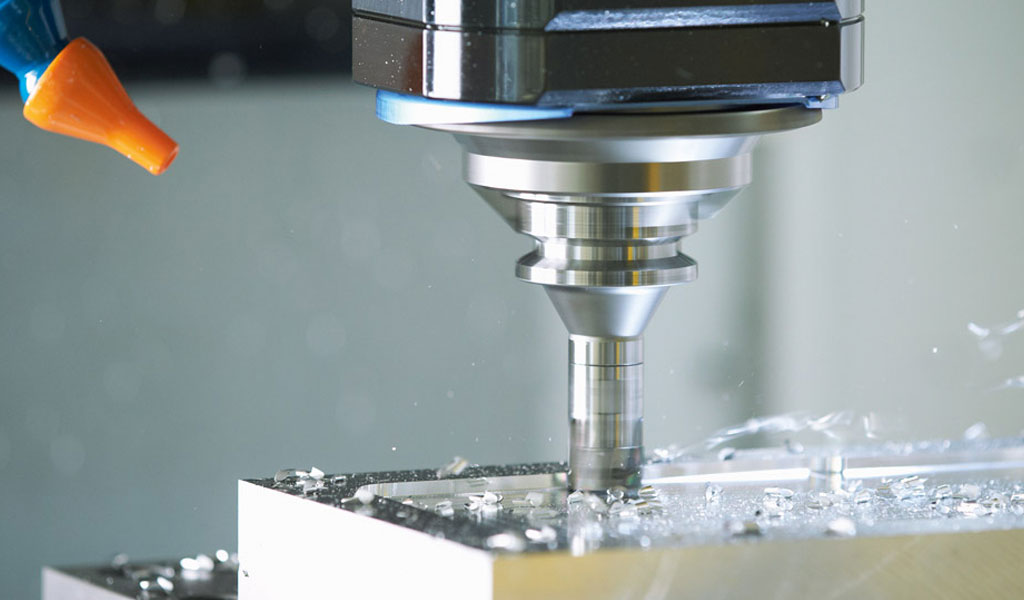

Metal CNC machining is a popular process used in the manufacturing industry for its precision and accuracy. CNC machines are computer-controlled tools that can cut, shape, and drill Metal block to create complex parts and components. This process is highly efficient and can produce large quantities of parts with consistent quality.
Understanding the basics of metal CNC machining can help businesses and manufacturers make informed decisions about their production processes and achieve better results.
What Is Metal CNC MachiningA. Definition of CNC Machining
CNC (Computer Numerical Control) machining refers to a manufacturing process that utilizes computerized controls and machine tools to precisely remove material from a workpiece. The numerical control aspect involves programming instructions into the CNC machine to dictate the exact movements, speeds, and depths of cuts required for creating a final product. This method replaces traditional manual machining processes, offering increased precision and efficiency.
Evolution of Metal CNC Machining
The evolution of metal CNC machining can be traced back to the mid-20th century when the first numerical control machines were developed. Initially used for aerospace and military applications, CNC machining(include 5 axis cnc machining and more) gradually expanded into various industries due to its accuracy and repeatability. Early CNC machines were limited in their capabilities, but advancements in computer technology and engineering have led to the development of highly sophisticated CNC machines capable of intricate and complex operations.
Significance in Modern Manufacturing
In modern manufacturing, the significance of metal CNC machining cannot be overstated. It has become a cornerstone technology that plays a pivotal role in producing a wide array of precision components across industries. The ability to achieve tight tolerances, create complex geometries, and automate production processes has positioned CNC machining as a driving force behind the efficiency and innovation seen in today’s manufacturing landscape. From aerospace and automotive to medical and consumer electronics, CNC machining is integral to the production of high-quality, reliable components. As technology continues to advance, CNC machining remains at the forefront of shaping the future of manufacturing processes.
Basics of Metal CNC MachiningA. Understanding CNC Machines1. Overview of CNC Machines
CNC machines are automated manufacturing tools that operate based on pre-programmed computer numerical control. They use coded instructions to control the movement of cutting tools and other machinery, allowing for highly precise and repetitive operations. CNC machines can be categorized into various types, each designed for specific applications and machining processes.
Types of CNC Machines used for Metal Machining
- CNC Milling Machines: These machines use rotary cutters to remove material from a workpiece. They are versatile and widely used for creating intricate parts.
- CNC Turning Machines (Lathes): Turning machines rotate a workpiece while a cutting tool shapes it. They are ideal for cylindrical and conical shapes.
- CNC Drilling Machines: Focused on creating holes in the workpiece, these machines are crucial for various applications, including aerospace and automotive.
- CNC Grinding Machines: Grinding machines use abrasives to remove material, providing high precision in achieving tight tolerances and fine surface finishes.
- Electrical Discharge Machining (EDM) Machines: EDM uses electrical discharges for machining electrically conductive materials, enabling the creation of intricate and delicate shapes.
Materials Used in Metal CNC Machining
1. Common Metals
Metal CNC machining accommodates a wide range of common metals, including:
- Aluminum: Lightweight and corrosion-resistant, suitable for aerospace and automotive components.
- Steel: Versatile and durable, used in various industries for its strength and machinability.
- Brass: Offers excellent thermal and electrical conductivity, often used for precision components
- Copper: Known for its conductivity, copper is utilized in electrical applications and intricate components.
2. Exotic Metals
In addition to common metals, CNC machining extends to exotic materials such as:
- Titanium: Lightweight and corrosion-resistant, commonly used in aerospace and medical applications.
- Inconel: Known for its high-temperature resistance, frequently used in aerospace and gas turbine components.
- Hastelloy: Exhibits corrosion resistance, suitable for chemical processing and marine applications.
- Nickel Alloys: Valued for their high strength and resistance to extreme temperatures.
CNC Machining Processes
1. Milling
CNC milling involves rotating cutting tools to remove material from a workpiece. It is widely used for creating complex shapes and features.
2. Turning
CNC turning, or lathing, rotates a workpiece while a cutting tool shapes it. This process is ideal for cylindrical and conical components.
3. Drilling
CNC drilling machines create precise holes in a workpiece, crucial for various applications, including assembling parts and creating pathways for fluids.
4. Grinding
CNC grinding machines use abrasives to achieve high precision in creating tight tolerances and fine surface finishes.
5. Electrical Discharge Machining (EDM)
EDM utilizes electrical discharges to erode material, allowing for the creation of intricate shapes and fine details in electrically conductive materials.
Advantages of Metal CNC MachiningA. Precision and Accuracy
1. Tolerances in CNC Machining
One of the key advantages of metal CNC machining is the ability to achieve incredibly tight tolerances. CNC machines operate with high precision, allowing for the production of parts with accuracy measured in microns. This level of precision is crucial in industries such as aerospace and medical, where components must meet strict specifications.
2. Surface Finish
CNC machining delivers superior surface finishes compared to many other manufacturing processes. The cutting tools used in CNC machines can create smooth and fine surfaces, eliminating the need for additional finishing processes. This advantage is particularly significant in industries where aesthetics and the tactile feel of the final product are essential.
B. Efficiency and Speed1. Reduced Lead Times
Metal CNC machining significantly reduces lead times in the production of parts. The automated nature of CNC machines, coupled with the ability to program complex operations, accelerates the manufacturing process. This rapid turnaround is crucial for meeting tight production schedules and responding swiftly to market demands.
2. Batch Production Capabilities
CNC machining excels in batch production scenarios. Once a program is set up, the machine can replicate the same operations across multiple workpieces with consistent precision. This capability is advantageous for industries requiring large quantities of identical or similar components, such as automotive manufacturing.
Versatility in Design
1. Complex Geometries
Metal CNC machining allows for the creation of intricate and complex geometries that would be challenging or impossible with traditional machining methods. The ability to produce complex shapes is particularly valuable in industries like aerospace, where lightweight and aerodynamic components are essential.
2. Prototyping Capabilities
CNC machining is a valuable tool for prototyping due to its versatility and ability to quickly transform digital designs into physical rapid prototyping. This accelerates the product development cycle, enabling engineers to test and iterate designs efficiently before moving to full-scale production.
Cost-effectiveness
1. Material Savings
CNC machining optimizes material usage, minimizing waste through precise cutting and shaping. This efficiency not only reduces material costs but also contributes to sustainability efforts by minimizing environmental impact.
2. Reduced Labor Costs
Automation in CNC machining reduces the need for extensive manual labor, leading to reduced labor costs over time. Skilled operators are still essential for programming and overseeing the process, but the efficiency gains contribute to overall cost-effectiveness in production.
Top 3 CNC Machining companies in Australia
1.Marand Precision Engineering
Marand engineers, manufactures and sustains complex innovative equipment and products for the aerospace, defence, mining, food, rail and energy industries with its customer base predominately blue chip companies such as Lockheed Martin, Boeing, BAE Systems, BHP & Rio Tinto. Australia’s largest privately owned Aerostructures manufacturer and F-35 Joint Strike Fighter exporter, Marand also has decades of experience in technology transfer, facilities design & build with automation and I4.0 solutions. The business offers total manufacturing solutions that encompass project management, design, manufacture, installation, commissioning, ongoing maintenance and spare parts support for any Marand supplied precision machine or product. The business is also complemented by Sister organisation Levett Engineering, a South Australian based supplier of precision components and assemblies for the defence and commercial aerospace industries.
- website:www.marand.com.au
- Phone:+61385520600
- Scale: 201-500 employees
- Headquarters:Moorabbin, Victoria
- Date of establishment: 1969
2.Romar Engineering
Romar provides advanced manufacturing solutions for a wide range of highly regulated industries including medical, aerospace, aeronautical, defence and automotive applications.
Our unparalleled manufacturing experience and the capability to provide scalable and commercially viable manufacturing solutions are what set Romar apart.
Our unrivalled knowledge of specialist areas like silicone manufacturing, precision molding, micromolding and medical device manufacturing ensures reliable, high quality outcomes.
And we excel at advanced manufacturing with state of the art equipment, including a Class 8 Clean Room, and the only Lasertec 65 3D printer in Australia.
- website:romareng.com.au
- Phone:+9644 5022
- Scale: 100-500 employees
- Headquarters:Moorabbin, Victoria
- Date of establishment: 1995
3.APEM
Our machine shop is equipped with HURCO machining centres takes machining to the next level. These machines deliver high performance capabilities to any machining application. Whether you are doing batch production or die/mould work, the VMX mills will make you more profitable.
We take pride in our specialised CNC machine tools and state of the art equipment. Our machinists are highly skilled craftsmen who have the ability to meet and exceed all your expectations. Whether it’s turning, milling we maintains a unique array of machine tools, and tooling and accessories to accommodate your most demanding machining requirements.
- website:https://www.apemgroup.com.au/
- Phone: 8605 1886
- Scale: 100-500 employees
- Headquarters:5 & 6, 78 Glendenning Road, Glendenning, NSW, 2761
- Date of establishment: No
Australia CNC Machining companies vs China CNC Machining companies
Comparing CNC machining companies in Australia and China involves considering various factors, including quality, cost, lead times, and manufacturing capabilities. Here’s a broad overview of some key points to consider:
Australia CNC Machining Companies:
- Quality Standards:Australian CNC machining companies often adhere to high-quality standards and certifications, ensuring precision and reliability in their products.Stricter regulations and quality control measures contribute to the reputation for producing high-quality components.
- Cost of Production:Labor costs in Australia are relatively higher than in countries like China, impacting the overall cost of production.However, Australia may be chosen for projects where quality and precision are paramount, even if costs are higher.
- Lead Times:Proximity to local markets can contribute to shorter lead times, facilitating quicker response to customer demands.Smaller geographical distances may result in faster shipping and reduced transportation times.
- Customization and Prototyping:Australian CNC machining companies are often preferred for customization and prototyping due to their ability to offer personalized solutions and close collaboration with clients.
China CNC Machining Companies:
- Cost of Production:China is known for its lower labor costs, making CNC machining more cost-effective for large-volume production.Economies of scale and a vast industrial base contribute to competitive pricing.
- Scale of Production:China has a large manufacturing infrastructure, allowing for mass production of CNC-machined components.The scale of production can lead to lower costs per unit for high-volume orders.
- Technology and Equipment: CNC machining china companies often invest in advanced technology and equipment, keeping pace with global manufacturing standards.The extensive use of automation contributes to efficiency and cost-effectiveness.
- Lead Times:Longer shipping distances may result in extended lead times for products shipped from China.However, many Chinese companies have optimized logistics to minimize delays
- Diverse Capabilities:China offers a wide range of CNC machining capabilities, from basic to highly complex processes, catering to diverse industry needs.
- Global Supply Chains:China plays a crucial role in global supply chains, making it a strategic choice for companies looking for a centralized manufacturing hub.
Considerations for Decision-Making:
- Project Requirements: The nature of the project, including volume, complexity, and required precision, will influence the choice between Australia and China.
- Budget Constraints: Consider the budget constraints and weigh them against the importance of factors like quality and lead times.
- Logistics and Shipping: Assess the impact of shipping distances and logistics on lead times and overall project timelines.
- Regulatory Compliance: Factor in regulatory and quality compliance requirements, which may be more stringent in certain industries and markets.
- Risk Management: Evaluate geopolitical and economic risks that may affect the stability of supply chains and production.
Ultimately, the choice between Australia and China for CNC machining will depend on the specific needs of the project, balancing factors such as quality, cost, and logistical considerations.
5 steps to create a cnc machining parts in China
Let’s take a look at the cnc machining process in China:
Step 1: Designing Your Product
This step includes the CAD drawings, PCBA schematics, and other design methods. You can design in-house or get a design firm to provide cnc machining parts concept design.
It is crucial that you own the blueprints and not your China manufacturer. Otherwise, they will consider it as their intellectual property rights.
Step 2: Ensuring the doability of the make or buy the materials
Then, you’ll need to conduct sourcing before making or buying the parts. Ensure to calculate the costs and consider the technical difficulties of cnc machining.
You should qualify suitable suppliers for the customization of product parts.
Step 3: Assembling Your cnc machining parts
You can start the assembly after the preparation of the necessary parts. There are several possible problems you’ll face. For instance, product ergonomics issues, aesthetic issues, performance issues, functionality issues, etc.
Various amendments and repetitions are often required to solve the main problems.
Step 4: Preparing Production Tooling
After approval of your cnc machining parts, you can then order the necessary tooling. For instance, the plastic injection molding and the testing equipment.
Try making some parts with your tooling and ensure that the result is desirable.
Step 5: Testing Your Product
Conduct in-depth testings and at least one pilot run before mass production. For instance, testing the product compliance, performance, key functions, and robustness.
It is better to discover the issues earlier to save fixing time and costs.
Highly Recommended CNC Machining Supplier From China: Be-Cu.com
Metal CNC machining is the ultimate solution for achieving precision and versatility in manufacturing. From aerospace to automotive, electronics to medical devices, the possibilities are endless. It offers high durability, lightweight properties, cost-effective production, and speedy turnaround time.
Metal CNC machining proves that technology and creativity go hand in hand. So, if you want to be ahead of the game, choose Metal CNC machining for your next project.
Be-Cu Is A Fabrication Company With Long History(Since 1995).In 2019, Leonard established a wholly-owned subsidiary Be-Cu Prototype to radically improve and satisfy the demands of global customers for the production of prototypes and tools from China.
On 30.000 sq.meter workshop space with employing over 200 skillful engineers and workers, we make over 5000000 piece high quality non-stanard parts a year to our customers all over the world. The ability to produce parts in China is in advanced level, strong engineering, high design capability and good communication skills.Short lead time, competitive pricing and long-term partnerships continues to be the success factors of BE-CU.
Be-Cu provides the highest standard of CNC machining service for all your needs. Contact us today to know more about what we offer!
sales: Bella
web:be-cu.com
Phone: +86 151 1280 7161
Email: info@be-cu.com
Affiliated: Be-cu Prototype
Address: Dongguan,China