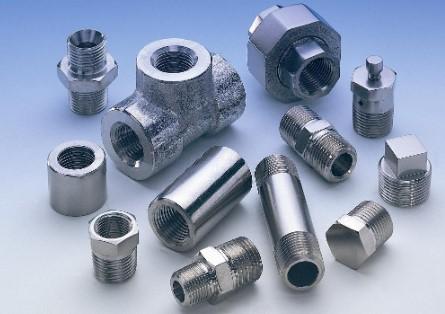
For industrial and plumbing systems to operate without interruption, pipe couplings are essential. These parts act as connectors, uniting two pipes’ worth of pipework to guarantee a steady flow of liquids, gases, or solids. To avoid leaks, maintain system integrity, and increase pipeline longevity, pipe couplings must be installed and maintained properly.

Installation and maintenance of pipe couplings
I. Installation of pipe couplings
A. Pre-installation preparation
Assessment and planning: It must be done to identify the type of a connection needed to fulfill the particular application before deployment. Measures must be considered regarding an assortment of variables like pipeline size, subject matter, the pressure, and temperatures.
Pipe preparation: A clean, straight, and defect-free pipe end is a must for proper pipe preparation. Debris, rust, and burrs should be removed in order to maximize the coupling’s performance.
B. Installation procedure
Selecting the coupling type: Compression couplings, threaded couplings, flange couplings, or any other form of coupling should be chosen depending on the application.
Proper alignment: Ensuring that the pipes being linked are precisely aligned is proper alignment. The performance of a system can be harmed by misalignment and leaks.
Tightening and torque: Follow the manufacturer’s instructions for torque requirements and tightening. The coupler can be harmed by overtightening, and leaks can occur from under tightening.
Sealing and lubrication: Apply the specified lubricant or sealing compound to create a solid, leak-free connection.
Quality control: Verify the coupling’s integrity and the lack of leaks by performing pressure tests as part of the quality control process.
II. Maintenance of pipe couplings
A. Regular inspections
Visual inspections: Check the couplings for wear, corrosion, or other damage on a regular basis. Try to spot any rust, cracks, or loose bolts.
Leak detection: Keep an eye out for any leaky signs, such as drips or stains left by water. To stop future harm, take immediate action if there are any leaks.
B. Preventive measures
Corrosion protection: Protect against corrosion by taking the necessary precautions, especially in corrosive settings. The lifespan of couplings can be increased by using coatings or corrosion-resistant materials.
Temperature and pressure monitoring: Monitoring of temperature and pressure: To prevent putting an excessive amount of stress on couplings, regularly check and maintain temperature and pressure levels within the advised ranges.
Replacement of seals and gaskets: In order to maintain a trustworthy seal, consider changing sealing components like O-rings or gaskets on couplings as part of normal maintenance.
C. Repairs and replacements
Prompt repairs: Repairs should be made right once if problems are found. This will help to avoid costly downtime and damage.
End-of-life replacement: Couplings have a limited lifespan. Once they show signs of wear and deterioration, which signify the end of their service life, replace them.
Advancing efficiency and reliability: Exploring advanced coupling technologies
The selection of coupling technology in the realm of fluid and gas handling systems is crucial for assuring effectiveness, safety, and dependability. A new generation of coupling technologies has emerged as a result of engineering improvements, notwithstanding the success of traditional coupling techniques. By boosting performance, streamlining installations, and lowering maintenance needs, these innovative couplings are transforming numerous sectors.
1. Quick-connect couplings
For applications requiring quick assembly and disassembly, quick-connect couplings are revolutionary. By enabling connections without the use of tools, these couplings cut down on labor expenses and installation time. Quick-connect couplings offer convenience without compromising on sealing performance, whether in industrial, medical, or automotive situations.
2. Grooved couplings
The strength and adaptability of grooved couplings make them highly valued. For a safe, leak-free connection, they depend on a mechanical groove and gasket. Due to their resilience in high-pressure and high-temperature situations, these couplings are especially well-liked in the mining, HVAC, and fire protection industries.
3. Push-to-connect couplings
The installation of hydraulic and pneumatic systems is made simpler by push-to-connect connections. The components can be pushed together to form connections by users using these couplings. This technique reduces the possibility of installation mistakes and guarantees trustworthy, leak-free couplings, making it the go-to option in sectors where accuracy and efficiency are crucial.
4. Smart couplings
Smart couplings are the way of the coupling technology future. These couplings offer real-time data on pressure, temperature, and flow rates since they are fitted with sensors and have Internet of Things capabilities. Predictive maintenance is made possible by this knowledge, minimizing downtime and enhancing system efficiency. Remote monitoring of conditions is a game-changer for efficiency and safety in essential applications like oil and gas pipelines.
5. Self-aligning couplings
It can be difficult to install pipes, particularly when doing so in small places or when joining materials that aren’t compatible. In order to solve this problem, self-aligning couplings allow for angular misalignment during installation. In construction and infrastructure projects, this feature makes pipes less stressed, increases their longevity, and makes installation simpler. As a result, it is a beneficial solution.

The effective and reliable operation of industrial and plumbing systems depends on the proper installation and maintenance of pipe couplings from https://www.dewaterproducts.com.au/ . These elements can be neglected without consequences, such as leaks, system breakdowns, and higher running expenses. Businesses and individuals can guarantee the durability and functionality of their pipelines by following best practices during installation and executing a preventive maintenance schedule. The future development of safer and more effective systems can also benefit from maintaining current with coupling technologies from dewaterproducts and materials. Although pipe couplings are relatively modest parts, the success of larger, interconnected systems depends on their appropriate maintenance.