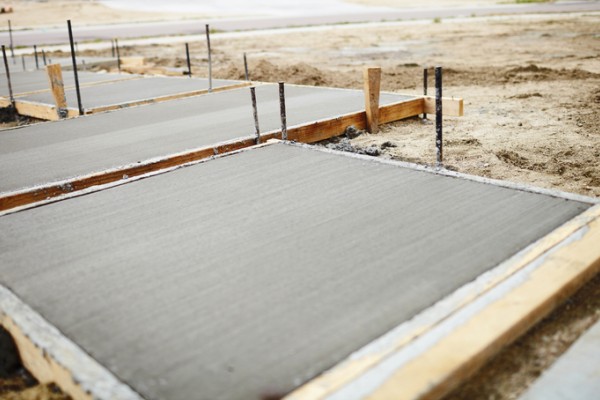
When building or extending a home, one of the most important early decisions is what kind of subfloor system to use. For homes on flat sites with stable soil, a ground-level slab is one of the most common and cost-effective choices.
Also known as a slab-on-ground, this type of subfloor offers a solid, durable base for the structure above. But like any building element, it needs to be designed and installed properly to perform well over time.
Here’s what you need to know about ground-level slab subfloors.
What is a ground-level slab?
A ground-level slab is a thick, reinforced concrete platform that sits directly on the ground and forms both the foundation and the floor of a home or extension. It’s poured over compacted fill and insulation, and includes steel reinforcement for strength.
This type of subfloor is typically used for:
- New homes built on level or gently sloping land
- Ground floor renovations and extensions
- Slab-based construction in areas with good soil conditions
Types of slab-on-ground systems
There are three main slab types used in residential construction:
1. Slab-on-ground with edge thickening (conventional raft slab)
This is the most common type of residential slab. The edges and internal footings are thickened to provide strength under load-bearing walls.
2. Waffle pod slab
This system uses polystyrene void formers (pods) as part of the base structure. Concrete is poured around and over the pods, creating a grid of beams. Waffle slabs are lightweight and quick to install, and often used in volume housing.
3. Slab with integrated beams (raft slab with ribs)
This slab has deeper beams integrated throughout the slab to add strength, making it suitable for reactive soils or heavier structural loads.
The choice of slab depends on soil classification, design loads, site drainage and bushfire or termite requirements. A structural engineer will generally be involved in determining the right system.
Compliance and standards
All slab-on-ground systems must be designed and built in accordance with AS 2870 – Residential slabs and footings. This standard outlines requirements for:
- Site classification (based on soil reactivity and drainage)
- Minimum slab thickness and reinforcement
- Movement tolerance and crack control
- Site preparation and compaction
Other relevant standards and codes include:
- AS/NZS 1170.1 – Structural design actions: permanent, imposed and other actions
- AS 3600 – Concrete structures
- AS 3798 – Guidelines on earthworks for commercial and residential developments
- NCC Volume Two – Housing Provisions, including Part 3.2.2 for slabs and footings
Slabs must also comply with termite protection requirements in AS 3660.1, particularly in high-risk areas.
Site preparation and drainage
Good site preparation is critical for a durable slab. The process typically includes:
- Clearing and levelling the site
- Compacting the soil and/or fill to the required density
- Installing formwork and reinforcement
- Adding moisture barriers, insulation or termite barriers as needed
Proper drainage is also essential. Poor drainage can lead to water pooling under the slab, which may cause cracking, slab heave or long-term structural movement—especially on reactive clay soils.
Slabs must be built with adequate fall and graded away from the building in line with AS 2870 and the NCC.
Benefits of slab-on-ground construction
- Cost-effective on flat sites compared to raised subfloors
- Quick installation, often poured in a single day
- High thermal mass, which helps with temperature regulation when combined with good passive design
- Solid feel underfoot, especially compared to timber floors
- Minimal risk of pest intrusion when combined with termite barriers
Limitations and considerations
- Not ideal for steep or uneven blocks—a suspended timber or steel subfloor may be more suitable
- Difficult to access services under the floor—planning is critical for plumbing and electrical
- Can be prone to movement on reactive soils without proper design and site prep
- Cold floors in winter without insulation—slab edge and underside insulation may be required in colder climates
Energy efficiency and insulation
The NCC now includes minimum insulation requirements for slabs where thermal performance is a factor in the energy rating. Insulation may be needed:
- Around the slab edges (slab edge insulation)
- Underneath the slab (underslab insulation), especially for waffle pod systems
- As part of a broader passive design strategy
Slabs used in combination with good orientation, thermal mass and shading can help improve a home’s energy efficiency under NatHERS assessments.
In summary
A ground-level slab is a reliable and popular foundation option for Australian homes, especially on flat blocks with well-drained soil. But as with any structural element, its success depends on good design, proper site preparation and compliance with all relevant standards.
If you’re planning a renovation or extension involving a slab, consult with your builder, engineer or designer early in the process to make sure the system you choose is fit for your site and fully compliant from the ground up.