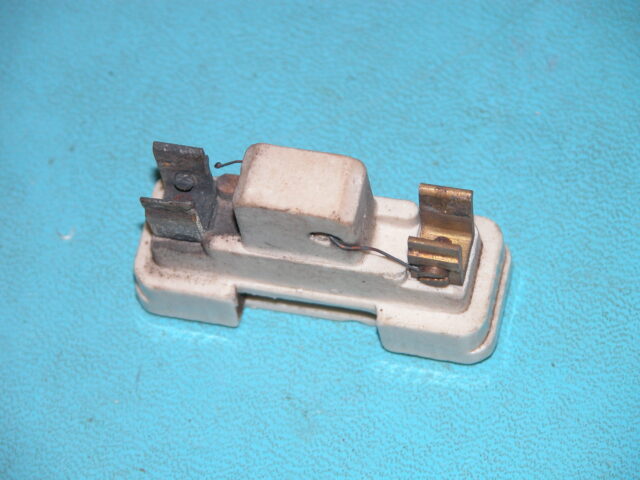
Jointing and terminating cables is an exacting business, writes George Georgevits. Following the requirements will ensure performance, safety and long service life.
Compression and mechanical jointing connectors rely on pressure to make an electrical connection with the cable.
They play a crucial role in service, are expected to have a long service life and may be required to handle high currents. Therefore correct product design, proper termination technique and product quality are essential for long-term reliability.
Connectors for insulated power cables
In general, such connectors are used for terminating or jointing cables. The type and size of connector is a function of the type and size of the cable and the amount of current the circuit is required to carry.
For power cables, there are additional performance requirements and limitations, including whether:
- the conductor material is copper or aluminium;
- the connector uses a mechanical clamp (eg: screw type) or a compression fitting (eg: crimp type) termination; and
- whether the connector is required to withstand a prolonged high intensity short-circuit current , such as may be encountered in electricity distribution networks where distribution circuits are protected by slow-acting protection relays rather than fast acting fuses.
The discussion here is limited to fixed jointing connectors intended for termination of insulated power cables.
Aerial cables, as used in overhead power reticulation networks, have additional special mechanical requirements. Similarly, separable connectors are another subject, although some of the test techniques may apply.
Standards
The applicable Australian Standard for connectors used with copper cables of cross-section area greater than 10mm2 and aluminium cables of cross-section area greater than 16mm2, is AS/NZS 4325.1:1995, Compression and mechanical connectors for power cables with copper or aluminium conductors, Part 1: Test methods and requirements.
This is based primarily on International Electrotechnical Commission Standard IEC 1238-1.
The Standard specifies testing of joint resistance after heat cycling, short-circuit testing (if applicable – depending on intended use) and mechanical ‘pull withstand’ strength testing.
A low and stable joint resistance is essential for good connector performance in the long term. The heat dissipated in the connector due to cable joint resistance may be calculated by multiplying the joint resistance by the square of the current passing through the connector.
If the connector is passing a current at – or more than – its rated current, a poorly terminated connector could easily have to dissipate much more heat than it is designed to do. This applies to the joint where the cable terminates inside the connector and also to the joint where the connector terminates on the equipment.
Extreme temperature rise may occur, causing connector oxidation and eventual failure – or worse.
High termination resistance at a joint is a common cause of switchboard fires.
A poor cable termination in a connector may be caused by:
- not using the correct tool or die for a compression connector (the die should be wide enough to properly crimp the connector over the required barrel length with a single compression);
- not applying enough pressure to perform the crimp action completely over the required barrel length – multiple short crimps along the barrel do not work as well as a single full-length crimp;
- not applying the specified tightening torque to a mechanical connector bolt;
- using the wrong size of connector for a given size and type of cable;
- using an aluminium cable crimp connector on a copper cable, and vice versa;
- not having the cable inserted along the full length of the barrel before terminating; and
- not ensuring that the cable conductor and the connector barrel are clean and free from oxidation and corrosion.
Testing to the Australian Standard
If a particular connector has been type tested and found to comply with the Standard, it can be implied that under normal operating conditions:
- the resistance of the connection will remain stable;
- the temperature of the connector will be of the same order or less than that of the cable conductor when in service;
- the mechanical strength will be fit for the purpose; and
- application of short-circuit currents, if the intended use demands it, will not affect the first three aspects.
The Standard defines an optional short-circuit testing regime. Only connectors that have been tested for compliance with the short-circuit performance requirements of the Standard (known as Class A connectors) are suitable for use in unfused applications, such as in power distribution and industrial networks.
Connectors that are not required to be tested for short-circuit performance are known as Class B.
Although the above is reassuring, it does not mean that a compliant connector will perform satisfactorily for all applications or under all conditions.
Prolonged elevated temperature, excessive vibration, shock or corrosion can have a detrimental effect on connector performance and shorten the service life. If connectors are exposed to such adverse conditions, appropriate additional testing may be required, as the circumstances dictate.
The range of connectors covered by the Standard includes both compression and mechanical jointing types. The realisations of both types include barrel or through connectors (for joining two cables), palm lugs (for terminating a cable on a busbar on terminating plant) and branch connectors (where one cable run is split into two).
Electrical compliance testing
In brief, the Standard calls for six terminated connectors to be tested.
The required connectors are terminated on stipulated lengths of appropriately sized bare cables, which are bolted together to form a test loop.
The test loop is subjected to heat cycling by passing a large AC current through it for a predetermined time, during which the conductor temperature is monitored.
For each cycle, the loop temperature is raised from room temperature to about 120oC, maintained at that temperature for 10 minutes then allowed to cool to room temperature.
The joint resistance of each connector is measured at the beginning of heat-cycle testing, then after specific numbers of heat cycles. Twelve sets of measurements are required during the stipulated 1,000 heat cycles.
Because the joint resistance for large connectors can be of the order of micro-ohms, accurate measurement of connector joint resistance is not straightforward.
To determine the joint resistance accurately, the AC heating circuit is disconnected and a much smaller but accurately controlled constant DC test current is injected into the test loop.
A high-precision DC voltmeter is used for measuring the voltage drop across each connector under test plus a predetermined and accurately measured length of test conductor immediately following each connector.
The DC voltage drop is also measured along a second separate but known length of test conductor (known as the reference conductor).
The resistance for each connector is then calculated by factoring out the voltage drops due to the relevant cable resistances.
The ambient temperature is also measured and is used for calculating the test results referenced back to 20oC.
For a connector to comply with the Standard, it must meet the performance parameters in Table 1.
The specific meaning and derivation of each of the above test parameters are complex and beyond the scope of this article. Readers should refer to the Standard. However, in simple terms, the requirements imply that the:
E.3 – spread for connection resistance of the six connectors under test must be within strict bounds at the start of testing.
E.4 – average values of the connector resistances for the duration of testing must be within strict bounds.
E.5 – variation in connector resistance during testing must be within strict bounds.
E.6 – maximum change in connector resistance as a result of heat cycling must be within strict bounds.
E.7 – maximum temperature reached by any connector during testing must be recorded.
Conclusion
Jointing connectors play a crucial role in long-term circuit reliability.
Testing of jointing connectors is a complex and involved procedure, and the Standard requirements are very demanding. Consequently, any connector which has been found to pass those requirements should provide reliable long-term performance.
Connectors used in critical applications should be type tested against the Standard.